How to turn plastic waste into recycled pellets?
Recycling and reusing waste plastic has become a hot topic in global environmental discussions. Transforming waste plastic into plastic pellets is a crucial process that breathes new life into discarded plastics, reducing environmental pollution. In this article, we will explore how waste plastic can be converted into valuable plastic pellets with plastic waste recycling machines.
Step 1: Plastic collection and sorting
Waste plastic can come from various sources such as plastic bottles, bags, containers, and more. The first step involves collecting and sorting different types of plastics. Common plastic types include PET, HDPE, LDPE, PP, and others. This step requires an efficient recycling system to ensure that plastics remain uncontaminated and free from impurities.
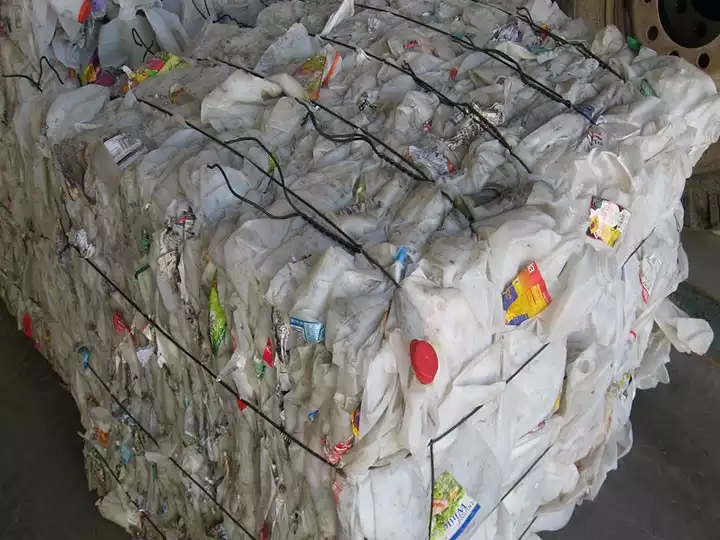
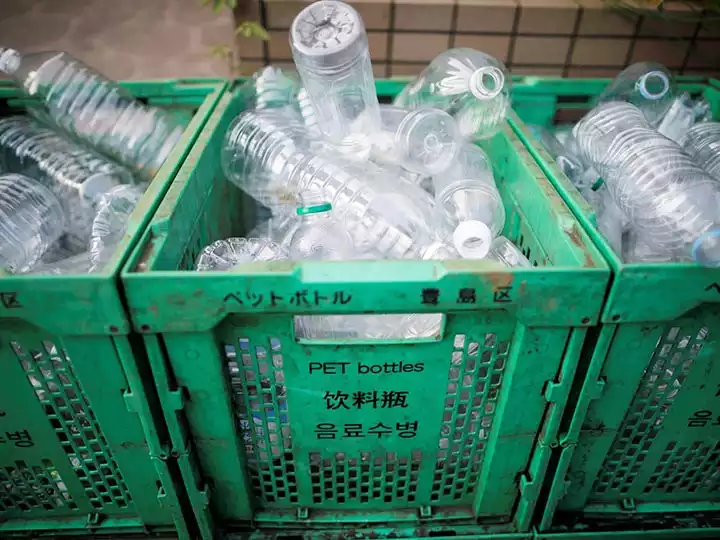
Step 2: Cleaning and removal of contaminants
Before plastic can be turned into pellets, it must undergo a thorough cleaning by cleaning machines. This includes the removal of dirt, labels, grease, and other contaminants. Cleaning can be achieved through mechanical and chemical methods. Cleaned plastic scraps are easier to process and yield high-quality pellets.
Step 3: Plastic shredding
The cleaned plastic is then fed into a plastic shredder, a crucial step in breaking down large plastic pieces into smaller fragments. The shredder employs sharp blades to cut the plastic into pieces. These pieces are often referred to as “regrind” or “regrind material.”
Step 4: Melting and extrusion
The regrind material is subsequently fed into a plastic pelletizing machine, which is the primary plastic waste recycling machine. Here, it is melted and extruded to form plastic pellets of specific shapes and sizes. This process requires high temperatures and pressures.
This is the most important stage of plastic recycling. Pelletizing is the process of melting down the plastic waste and forcing this through a plastic pelletizer. The plastic is extruded as it comes out of the pelletizer machine to form pellets.
Step 5: Cooling and Cutting
The newly formed plastic pellets require cooling after extrusion. Cooling can be achieved using water or air, ensuring that the pellets maintain their desired shape. Subsequently, the pellets are cut to the required length.
Step 6: Packaging and Sales
Finally, these plastic pellets are packaged in bags or other containers and prepared for sale. They can be used in various industries, including manufacturing plastic products, textiles, packaging materials, and more.
Conclution
Transforming waste plastic into plastic pellets not only aids in resource recycling and environmental protection but also provides high-quality recycled raw materials for manufacturing. This process necessitates advanced plastic waste recycling machines, making the selection of a reliable plastic recycling machine manufacturer crucial.
If you are interested in entering the plastic recycling business, understanding these steps and contact us now, we will contact you and send you machine details within 24 hours.